Welding in general, is a costly, time-consuming and labor-intensive process that is the accepted normal practice when managing and installing metal pipe penetrations onboard marine vessels and offshore platforms.
However, developments in tested and approved pipe penetration seals are making the accepted normal practice of welding everything in sight, a thing of the past.
Heavy-duty pipe systems
Historically, for thick walled metal pipe there has been the process of welding it directly to the structure on both sides of the deck or bulkhead or utilizing a heavy and thicker walled penetration piece that may either be purchased or self-fabricated.
Both these systems require a significant amount of welding with either two or possibly four different welding joints. However, options are now available which can significantly reduce and even eliminate the need for any welded joints when passing metal pipe through any fire rated deck or bulkhead.
Dissimilar metal pipe systems
With the growth in use of thin walled (less than 3mm) metal pipes such as stainless steel, copper, CuNi and even titanium, welding requirements and the levels of technical skill required to weld and manage these pipe penetrations have also grown.
The high costs associated with these increasing levels of welding can be completely erased by a change in process, and a change in thinking about how to manage metal pipe penetrations.
The traditional methods of transitioning to bulkhead unions, steel pipes via flange or coupling connections or through sleeves or coamings, are gradually being replaced within the industry by alternative solutions that do not require any welding at all.
Zero welding for these dissimilar metal pipe installations is a significant benefit in its own right however, additional benefits also exist by not transitioning to steel pipe at each penetration.
Benefits such as, not compromising the integrity, quality and performance of the pipe system by changing from your chosen, technically superior thin walled metal pipe of choice, to a low quality steel pipe at every deck or bulkhead penetration.
Repair and retrofit projects – hot work permits
During a retrofit or repair project, the logistics, manpower level and practical steps required to obtain, monitor and implement a hot work permit are significant. By limiting or removing the need for any hot work, simple time management cost savings which contribute to the project being delivered on time, should be enough to justify a switch from traditional welding solutions. Other savings are also generated, such as installation time, labor rates and other associated costs.
Roxtec’s alternative solution
Roxtec metal pipe seals can manage single (up to 558mm / 20”) and multiple (up to 54mm / 2”) metal pipe penetrations by utilizing a sleeve or coaming which can either be bolted or installed via a compression unit.
Both installation techniques provide the same fire rated benefits as traditional welded solutions in addition to significant water and gas tightness levels without the need for any welding.
These alternative solutions to welding pipe penetration seals offer qualified levels of safety and certified performance and are recognized and approved by all leading classification societies.
If you have previously identified the benefits of non-weld solutions or simply have a desire to reduce welding during new-build and repair or retrofit projects, metal pipe penetration sealing solutions could be the opportunity you have been looking for.
Roxtec invites you to investigate further, the multiple non-weld solutions we have in our product portfolio and start enjoying the benefits and cost savings associated with managing your metal pipe penetration seals with zero levels of welding, as soon as possible.
Author
Will Hoffman
Pipe sealing specialist Department Business Area Marine & Offshore at Roxtec
Product data
Find ratings, certificates and available sizes in our product database.
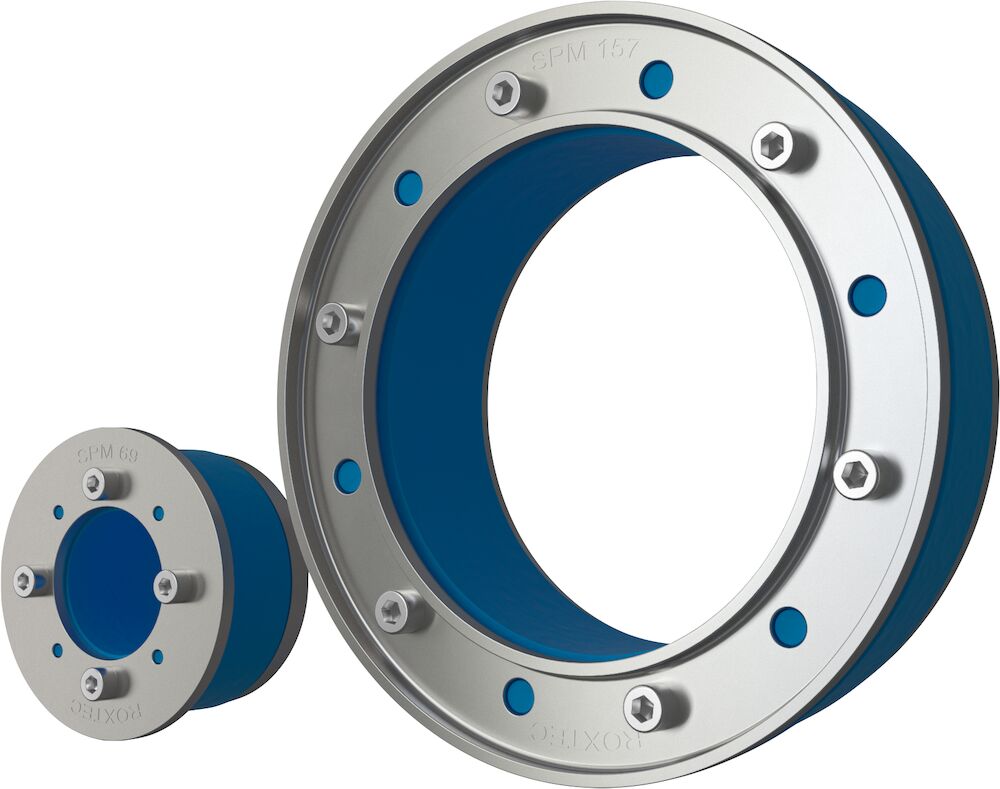
Roxtec SPM™ seal
Seal for metal pipes for use when welding is not allowed, recommended or desired.
Easy installation without weldingInterested in a test installation?
Fill out the form and we will contact you for a product demonstration or test installation
Thank you for contacting us!
We will get back to you shortly.
Best regards,
Roxtec
